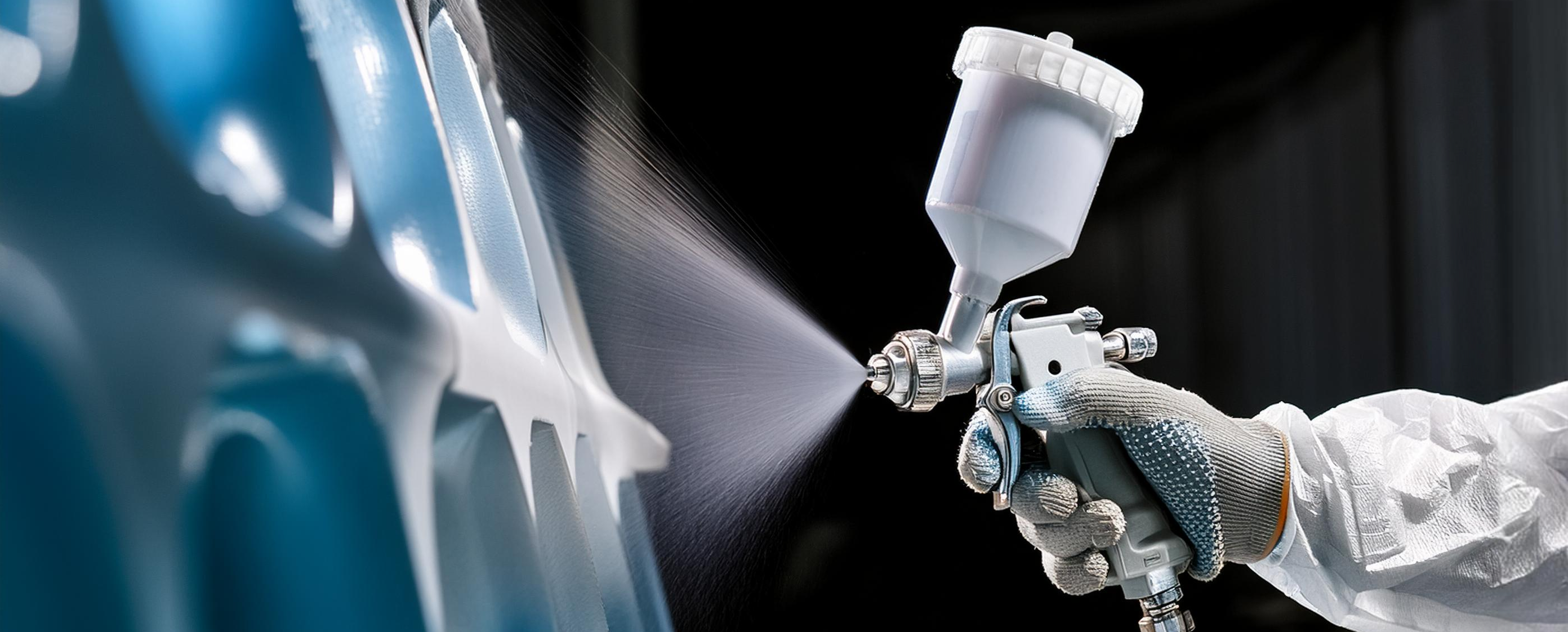
Coating
Effective protection and finishing thanks to customised coating solutions for plastic molded parts
Plastic molded parts
Coating
Coatings have become an integral part of modern manufacturing and industry. They not only offer added aesthetic value, but also functional protection and durability for a wide range of products. Depending on the application and requirements, different types of lacquer are used, each of which is characterised by its specific properties.
- Visual effect (colour tone, gloss level, effect appearance)
- Mechanical resistance (abrasion, impact/shock, deformation)
- Chemical resistance (alkalis, acids, solvents, hydraulic oils, coolants)
- Climate resistance (indoor/outdoor climate, outdoor climate)
- Special requirements (e.g. printable using pad or screen printing, weldable, bondable)
- Coating as a functional surface
Top coats
Conductive lacquer
Conductive lacquer is a special type of coating that serves as a functional surface to ensure the electromagnetic compatibility (EMC) of electronic devices. This coating minimises electromagnetic interference and meets the requirements of the European EMC Directive and international regulations. By using conductive coating, manufacturers can ensure that their devices comply with strict EMC requirements while improving the functionality and safety of the devices.
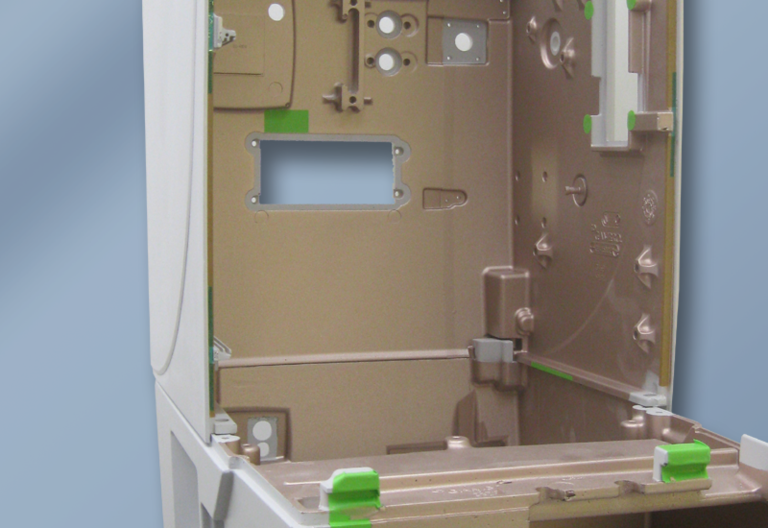
- Electromagnetic compatibility (EMC)
Conductive paint helps to ensure the electromagnetic compatibility of devices by shielding and dissipating electromagnetic interference. - Different types of conductive varnish are used depending on specific requirements such as frequency, intensity and location.
- Application on the inside: The conductive lacquer is applied to the inside of the molded part to avoid adhesion problems with the top coat.
- Masking: Masking ensures that air and creepage distances are maintained and the contact surfaces of the component interfaces remain conductive. This closes the ‘Faraday cage’ of the device.
- Low-resistance connection: A large-area, low-resistance connection of the moulded parts is already taken into account during the development phase in collaboration with the customer.
Cooperation with paint suppliers
For each application, we work with our paint suppliers to develop the optimum and most economical coating proposal in terms of function and quality.